There is much that can be done to ensure you are designing and installing the most energy efficient air handling system available, says Craig MacFadyen
The Energy Performance of Buildings Directive stipulates that both energy efficient design and the efficiency of ongoing performance are paramount requirements. Without doubt, this sets higher standards for air handling appliances, so not only do the units need to offer more efficient performance, but they also need to be easier to maintain, minimising life cycle costs.
There are two aspects of energy with regard to an air handling unit (AHU). First, there are the component parts of the AHU which can be designed to be highly efficient and hence reduce the energy required to supply the HVAC system with the air it requires. But there is also the energy recovery side which has an even greater effect on the system energy use.
Beginning with components, we can start with the heart of the AHU, the fan/motor set.
There has been a move in recent years from a belt-drive centrifugal fan solution to the direct-drive centrifugal fan (often referred to as a plenum or plug fan).
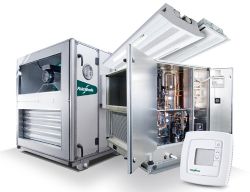
Rising price of energy
This impetus in the change-over process from belt-drive to direct drive has been pushed with the rising price of energy and the standardisation of invertors on fans, and now that the market is more aware, the trend is likely to accelerate.
Add to this the ability to reduce the footprint of AHUs, decreased maintenance (with no belts to re-tension and replace and no belt residue to clean up) and a reduction of downstream filtration requirements, and the adoption of direct-drive options will clearly become a driver for change.
Motor technology is also moving on at a pace and IE4 motors are now becoming more commonplace. These are far more efficient than IE2 motors that are required in most specifications and will contribute to significant energy savings.
An inverter also has an important part to play if maximising energy savings of AHU is to be realised. The use of a frequency inverter provides control opportunities not available with belt-drive systems, and when the cost comparison is made including capital cost, installation, balancing, commissioning and lifetime operating costs, the inverter-driven, direct-drive, plugfan solution becomes very attractive.
Technological advancements have become commonplace, and one development has been the use of in-built controls to optimise AHU performance.
The controller is a complete digital control system for most common AHU configurations, including single zone, variable air volume, multi-zone, and dual duct. It is designed to reduce energy usage while keeping occupant comfort its top priority in both new construction and retrofit applications.
Ideal for standalone operation, it can also communicate with a building management system, flawlessly providing all point and control information to the rest of the network. It can also be configured as a generic loop controller for unique applications.
The final 'must have' component to maximise the effectiveness of a system is an integral cooler. In business and office spaces, lighting, apparatus and people all represent a heat load.
So, for an even and comfortable room temperature of 21- 24 deg C, the need for energy for cooling is greater than that for energy for heating. Supplementary cooling is necessary and cooling can be achieved economically using an integral cooler. The cooling comes from the extract air being used to remove heat from the condenser. As this air is generally cool, the coefficient of performance (CoP) of the cooling machine is very high (normally in excess of 4.5).
Integral coolers replace other components, such as liquid coolers and external condensers and take up far less space. As it is included into the air handling unit, all components are located in the plant room, avoiding outdoor or roof installation. Because the appearance of a building is not changed, renovation work is easier, and noisy condenser fans are not necessary.
Moving onto energy recovery devices, these have become vital in the battle to eliminate energy use in HVAC systems.
Energy recovery trend
When compared to traditional crossplate heat exchangers or run-around coils, thermal wheels are now the leading component in a trend towards energy recovery.
Thermal wheels have the capacity to turn a standard-efficiency air handling unit into a high-efficiency unit, with the consequent energy savings and the reduced carbon emissions that implies. Thermal wheels can recover about 75-85 per cent of the energy from the extract air, transferring it to incoming fresh air, which then needs minimal additional heating to reach the required temperature for the building. In fact, a 75 per cent efficient thermal wheel operating in London will reduce the heat demand, from boilers or otherwise, by 95 per cent compared with a unit without energy recovery.
Given the strict legislative requirements for energy efficiency and the benefits they offer, it is hard to imagine AHUs in the future being installed without some form of integral energy recovery. Thermal wheels do the job more efficiently than most, and can have a significant positive impact on carbon footprint and fuel costs.
However, it is only when the components are put together in a well thought out manner, that we can really obtain energy efficient systems. By using the integral cooler, with a thermal wheel, we can achieve cooling CoPs of up to 11.
This is done by clever placement of the evaporator and condenser and controlling it with the thermal wheel to maximise cooling recovery.
This really is the future of air handling.
//The author is applications manager at Flakt Woods //