James Townley, technical sales manager at ENWA, insists that to ensure maximum return and lifespan from new technology, building services engineers cannot afford to overlook the water
THERE has never been a better time to consider the health of your HVAC system. If the new building regulations are just starting to pinch, the prospect of future energy prices threatens to bite even the smallest operator.
With this in mind, the industry has seen a massive programme of refurbishment, primarily of heating systems, with the installation of condensing boilers and improved building management systems the significant developments. Water treatment proposals often fare well during this period, as the poor internal condition of existing plant and high costs of replacement are never closer to the client's mind.
It is worth taking this retrospective view when considering water treatment for new builds, where conflict between initial capital expenditure and longer term operating costs can arise. Even under the PFI approach, where responsibility for future management of the building can extend to 30 years, this is not entirely eliminated.
Undetected losses of system water, high turnover of maintenance personnel and changes of building use can exert pressures which can undermine the continuity and effectiveness of the water treatment regime and threaten the performance and efficiency of HVAC systems.
The issues
The key issues in closed systems are corrosion, scaling and bacterial growth. These can impact directly by reducing heat transfer efficiency, restricting flow and seizing moving parts. Long term exposure can lead to degradation of components and an ongoing schedule of replacement. However, it is the generation of particulates arising from these processes that often causes the most problems. Entrapment in narrow or low flow areas can further disrupt flow rates, impair valve function and increase erosion. Figure 1 shows a breakdown of typical heating system faults that will be familiar to many operators.
Efficient operation is based on maintaining correct flow rates, pressures, heat transfer efficiency and flow and return temperatures. The presence of one or more faults will lead to a deviation from the original design parameters. Temperature control within buildings can become uneven, with boilers or chillers striving to reach set points through longer and more frequent operation. Impaired function of automated valves, short circuiting of flows and increased pump workload can all impact significantly on energy consumption. This is illustrated in Figure 2, which shows a recent study with Aberdeen City Council. Water treatment units were installed in five sheltered housing properties before the 2004 / 2005 heating season. Energy consumption was compared with 20 untreated properties across the city. By adjusting each site to a common comparative index at the start of the trial, a clear difference emerges. On average, consumption of oil and gas in treated properties was 8% below the control group.
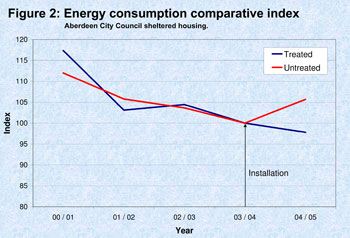
Rapid return on the investment in water treatment is possible where savings in both energy and maintenance costs can be made. The 8% energy reduction in this example would represent a mean annual saving of £2,500, providing payback in one to two years. Reductions in maintenance costs (Figure 3) could easily exceed this figure, while annual water treatment cost is less than £200 per site.
Poor performance can have other costly consequences. Reliability of delivery can be a critical factor, whether it is heating for elderly residents or cooling for a battery of data storage servers. Health and safety considerations are never far away, with the structural integrity of plant containing water at high temperatures and pressures representing a serious concern.
The key is replacing expensive and stressful reactive maintenance with long term, planned preventative maintenance.
Successful water treatment must likewise address immediate and future concerns.
The traditional specification of a dosing pot for chemical inhibitors becomes less effective over time and may be of little value in older systems where internal surfaces can no longer be effectively treated. Initial high concentrations of chemical inhibitor or biocide can, in practice, become diluted, demanding frequent testing. A smarter dosing arrangement that can respond to the quantity of make-up water and /or quality of the system water should be incorporated.
No form of chemical additive can work if the system is not physically clean. Current building services guidelines recommend employing side stream filtration as soon as possible, assisting with commissioning of new build and refurbished systems and ensuring their long term health. Figure 3 highlights the rapid restoration possible following installation of a combined side stream filtration and water conditioning unit.
Building services design and the components employed are becoming increasingly sophisticated. To ensure maximum return and lifespan from new technologies it is vital not to overlook the common denominator in most systems - water.