Lindab's Andy Watton believes the building services industry is far too complacent about the high rates of air leakage we are seeing from our ductwork systems.
'Love,' wrote the poet, 'free as air.' Well today love may or may not be free, but air most certainly isn't, at any rate not the air that circulates in the environmental control systems serving our commercial and public sector buildings.
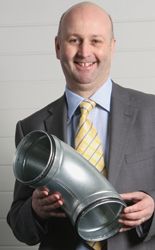
Andy Watton, Lindab
Those systems require fan power and the UK's relaxed attitude to ductwork leakage is wasting far too much of it.
Designers and manufacturers devote enormous ingenuity and investment to developing energy saving fan solutions.
And yet, if we allow air to leak from ductwork at the present rate, those solutions are just ever more sophisticated locks for a stable door through which the horse has long since bolted.
For a true measure of the efficiency of any system the transfer losses need to be taken into consideration and, in a ventilation system, this means duct leakage.
The accepted rates of duct leakage are laid out in HVCA's DW144 and range from class A to class C, where C is the tightest leakage class.
The rates allowed for a class A system permit nine times more air leakage than class C with a corresponding rise in the amount of fan power required to make up the losses.
What other branch of building services would tolerate wastage at these levels?
Waste of energy
It gets worse. In addition to the additional energy consumed by the fan, energy used in generating heating and cooling is also wasted and is directly proportional to the ratio of the leakage. So, moving up from a class A system to a class C system would represent an additional saving of 8 per cent of heating and cooling energy consumption.
It's been calculated that if all European ducting systems were truly airtight, we could achieve an annual energy saving equivalent to the annual output of three nuclear power plants.
It's a big problem but one to which a solution is available.
The technology to achieve class C as an industry minimum standard for circular ductwork is already available and at cost effective prices. Obviously, I'm most familiar with my own company's product. However, there are others, each offering their own special features, but sharing the environmental benefits being made from fully recyclable steel and requiring no sealant or tapes.
Lindab's Safe System circular ductwork offers a class C system straight out of the bag. With the correct installation techniques class D can be achieved - a 27-fold increase in air tightness over class A. Its double lipped EPDM sealing system ensures an airtight fit to minimise duct leakage.
As a result energy efficient fans can be just that - energy efficient.
In addition to saving energy, the system requires no sealant or tapes and as a result no 'curing time' is required. This means that it can be installed and pressure tested the same day, eliminating return visits to site, reducing costs and cutting out additional CO
2 generating journeys.
The health and safety issues associated with using solvent based sealing products on site and the environmental impact of the empty tubes disposal are also alleviated.
How many of us could pass a running tap without trying to turn it off? Air leakage is invisible and pretty much silent, but the cost in environmental terms is cold hard fact. We have the technology to make ductwork virtually airtight. Let's put it to work.