Trevor Dann, operations director of The ThermoGroup, offers end-users of older chillers monitoring with potential savings which could become apparent in just a few weeks.
Under Part L of the building regulations it is a statutory requirement for those installing new comfort cooling equipment in new or existing buildings that such equipment must meet a minimum defined standard of operating efficiency. However, once such plant is installed there is little further obligation or emphasis placed upon building users to ensure the plant achieves this minimum when newly fitted, or ensure this standard is maintained or improved upon during the operational life of the equipment.
Even if chillers are properly installed, invariably as cooling equipment ages it may not break down but does not work as well as it did. Whether this arises from poor design, lack of maintenance, poorly undertaken maintenance or repairs, or simply the primary desire, as is so often seen, to minimise repairs costs, is not always apparent.
However, cheapest is not always most economic. Where energy is concerned, the water chillers in many buildings will be the largest load and, sadly, the most misunderstood and often most neglected when it comes to optimisation.
What astounds us at ThermoGroup is that a simple energy hit with the largest load results in a massive saving, but often this is considered of secondary importance to short term cost savings in getting a repair project completed properly.
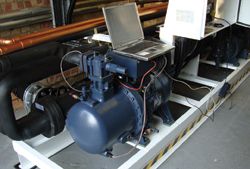
Monitoring a bespoke chiller
Sadly, the newer rules for inspection of air-conditioning systems in complex buildings pay little, if any, attention to the efficiency of larger cooling plant such as chillers.
However, as this is likely to be probably the single largest load demand on many buildings we believe techniques to help users further are vital, especially as improvements to the energy performance will easily offer a payback, sometimes within weeks or even days.
As part of our Re-Chill concept chiller upgrade package, ThermoGroup has developed the retrofit ThermaTech Magnum controls system applied as part of the various project techniques utilised, to provide real-time read out of the chiller cooling duty and energy efficiency ratio (cooling duty achieved v power absorbed).
So, at a glance, building users with ThermaTech Magnum can now find out the current energy efficiency of their plant.
Magnum generates the raw data to establish the cooling duty anyway, and to approximately 5 per cent accuracy.
By separate use of a dedicated power meter as also required under Part L, the data from both is combined to provide the energy efficiency in real time on the primary chiller display panel.
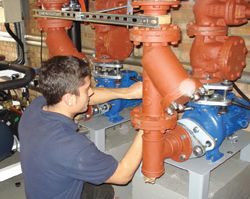
A Thermogroup engineer installing a bespoke chiller
Accurate knowledge of the EER of a chiller or group of chillers can provide a major advantage to users to allow optimisation of the chillers to reduce their energy consumption. Also, when a chiller becomes older and less reliable it may not simply trip out but soldiers on, with far-reduced energy efficiency.
The user is left in a false state of security as the unit does work in its basic function, and may indeed avoid the direct costs of servicing the chiller when, in fact, this cost could be far less than the increased energy bills resulting from poor operating efficiency.
Real-time EER is one of the developing features offered as part of the Re-Chill package of techniques to improve older and less reliable chillers. This technique can equally be applied in any situation where energy consumption is a focus issue.
The controls system which ThermoGroup uses for retrofit offers many other significant benefits for our Re-Chill projects such as a high level of compressor protection, maximised chiller availability, with self limiting load in high ambient conditions, multi mode motor protection, even low compressor superheat and low system sub-cooling are monitored for abnormal operation.
Magnum can currently support 104 separate inputs, outputs and indeed analogue outputs, which allow easy control of any four circuit chiller with both variable speed fans and electronic expansion valves.
Energy efficient operation for multiple circuit chillers can also be widely assigned via the multitude (over 350) programmable set points and set up options.
Magnum comes into its own realm when processing the complex issue of screw compressor slide valve regulation. Unlike many other chiller controllers, Magnum is directly programmed to respond to the specific load curve of the particular screw compressor installed on each individual sub-system, and can produce load algorithms for virtually any make or model of compressor.
This allows positive yet gentle control of the slide valve across the load range and provides for highly stable and efficient system optimisation, again in real-time.
If you need improved chiller control, would like to know more about real time energy monitoring or ThermaTech Magnum, ThermOzone can be contacted on 0118 950 0606.