Getting the commissioning wrong can mean the difference between an air conditioning system working perfectly, or not working at all, says Martyn Ives
Some people think the commissioning of an air conditioning system is something you do after the installation, when it is as much part of it as correctly positioning the units.
One problem is that there can be a great deal of pressure on contractors from end users, who often do not understand what commissioning is, to rush the process. The end user sees that all of the equipment has been installed and the power connected, and cannot understand why it is taking so long for him to enjoy the benefits of his new system, but without carrying out a thorough, methodical commission process, the system may not work as designed.
This is a plea to contractors to spend the right time going through that methodical commissioning process and for end users to allow them the time.
Steps to optimum performanceIn my view, there are five main steps to ensuring an air conditioning system works to the optimum: design, installation, commissioning, operation and maintenance.
Each step is as important as the other and the correct amount of time should be allocated for each stage.
Even something as basic as calculating the additional charge correctly is very important. Overcharging and undercharging will cause the system to run inefficiently and in some cases to malfunction.
Addressing the system, so the indoor units will talk to the outdoor units properly, can be one of the areas of commissioning that gives the most problems when the equipment is switched on - and the larger the system, the more involved the process.
While VRF systems are simpler to commission than they were, it is still worth double checking that all the units have the right address, as incorrect addressing can result in the end users thinking they are changing the settings for a wall-mount in office A, when they are really adjusting the ducted unit in showroom B. Much confusion ensues and the result is a dissatisfied customer and an unnecessary, unbillable callout.
Many systems offer auto-addressing as well as manual, but auto-addressing does not address in a logical way, so rooms next to each other can be wide apart in the numbering system, which just adds an extra complication for the service engineer.
To help with commissioning, Fujitsu offers a powerful piece of software called Service Tool, which allows the commissioning or service engineer to check that all address settings are correct, view all temperature and pressure readings from condensers. It also monitors running currents, valve controls, compressor frequencies, amps, and fan speeds. On the indoor units it can monitor temperatures, fan speeds, valve control and operation mode.
For those installers who are worried about the commissioning process, or simply do not want to tackle it, we, like other manufacturers, provide a commissioning service and commissioning training courses.
Not all aspects of commissioning are quite so technical an operation, requiring someone who has been fully trained, many of the time-consuming parts are very basic, but still need doing thoroughly.
For example, it is imperative to ensure the installation is correct to the design schematics supplied by the manufacturer. Visual checks need to be made on all pipe work and fittings before the builder makes them inaccessible, ensuring the pipe work is supported correctly and well insulated, separation tubes and refrigerant branch boxes are installed at the correct angle as shown in the installation manual.
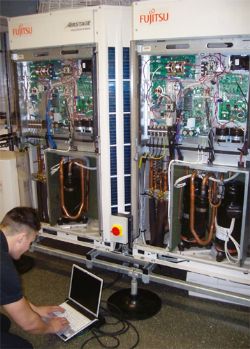
No unwanted noise
Even more low-tech is checking that the system is achieving the right temperatures and there are no noises that should not be there.
As well as the mechanics and electronics of the system, to my mind, it is just as important to ensure the human element is working properly and will continue to function into the future. In other words time needs to be taken to show anyone who is likely to be able to adjust the controls, how to do it properly without causing more problems. Contractors should also assure themselves that the end users know who to contact if things go wrong and how to get hold of them.
This is more than just running Fred(a) the office manager through the basics in five minutes flat and ignoring the blank expression; it requires producing clear concise written instructions that stay with the system and can be used by whoever takes over when Fred(a) goes on holiday or leaves. When a system gets messed up by an end user, it is the system or the installer that gets the blame, not the end user. Carrying out a proper handover is simple self-preservation.
Unreasonable prejudice
Finally, we live in a world where there are many people who have an unreasonable prejudice against air conditioning. I am not talking about environmentalists, but the people that are to be found in all offices.
The ones who say 'it gives me a dry throat', 'there's a draught that gives me a neck ache', 'I always have to bring a sweater to work because it's too cold', and so on. We've all met them, and often their complaints are valid, but they blame air conditioning as a whole, when the problems are usually down to a failure of the commissioning process, or wrong settings that have crept in since, because of a
failure in the handover.
We all have a duty to sell the benefits of air conditioning, that is how we make our living, and the first step is to ensure that those using our products are so happy with their systems that they spread the word to other potential customers and return to us when they need new systems.
A good commissioning process is the seed of tomorrow's market growth.
// The author is technical manager of FG Eurofred //